Ultimate Checklist for Sourcing the Best Hyd Pumps for Your Projects
In the rapidly evolving landscape of industrial applications, the demand for high-quality Hyd Pumps has surged, driven by advancements in technology and the need for enhanced efficiency. According to a report by MarketsandMarkets, the global hydraulic pumps market is projected to reach USD 15 billion by 2025, growing at a CAGR of 5.3%. This growth underscores the importance of selecting the right hyd pumps for any project, as they are crucial to the effectiveness and reliability of hydraulic systems. However, with a plethora of options available, sourcing the best hyd pumps can be a daunting task. To streamline this process, it is essential to adopt top strategies that not only ensure optimal performance but also align with your project’s specific requirements.
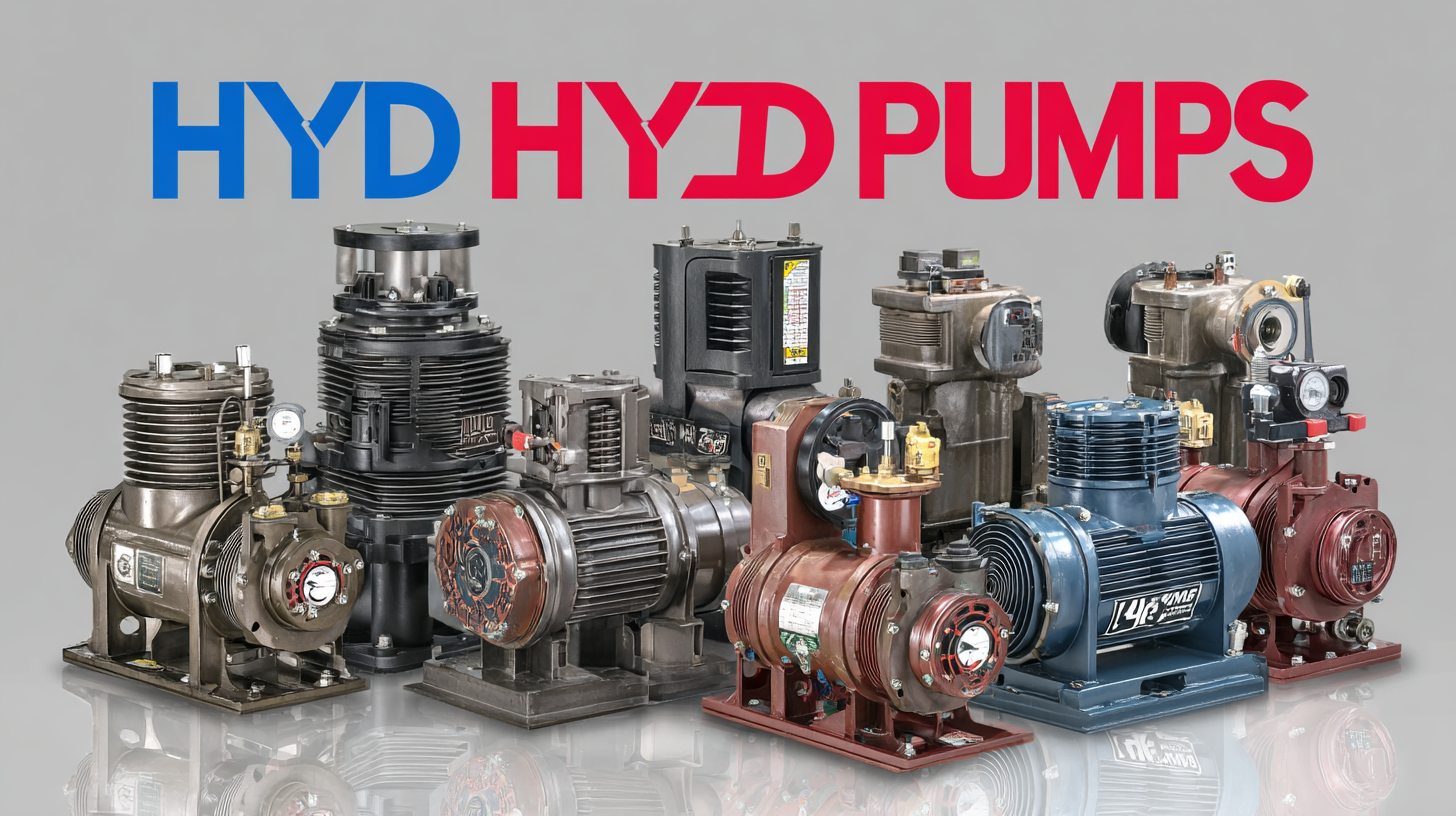
In this ultimate checklist, we will explore key considerations and best practices for sourcing exceptional hyd pumps that will enhance productivity and deliver superior results.
Understanding the Different Types of Hyd Pumps Available in the Market
When sourcing the best hydraulic pumps for your projects, it is crucial to understand the various types available in the market. The global hydraulic pumps market is projected to grow significantly, with an estimated value of USD 18.6 billion reaching by 2035. This growth is primarily driven by the increasing demand for efficient hydraulic systems, particularly within the industrial automation and machinery sectors.
Among the different types of hydraulic pumps, axial piston pumps and gear pumps are notable for their efficiency and versatility. Research indicates that the Axial Piston Hydraulic Motors and Pumps market is expected to rise from $2.9 billion in 2023 to $4.7 billion by 2033, showcasing a CAGR of 4.8%. This underscores the importance of selecting the right type for specific applications to ensure optimal performance. Understanding these dynamics can guide you in making informed purchasing decisions that align with your project requirements.
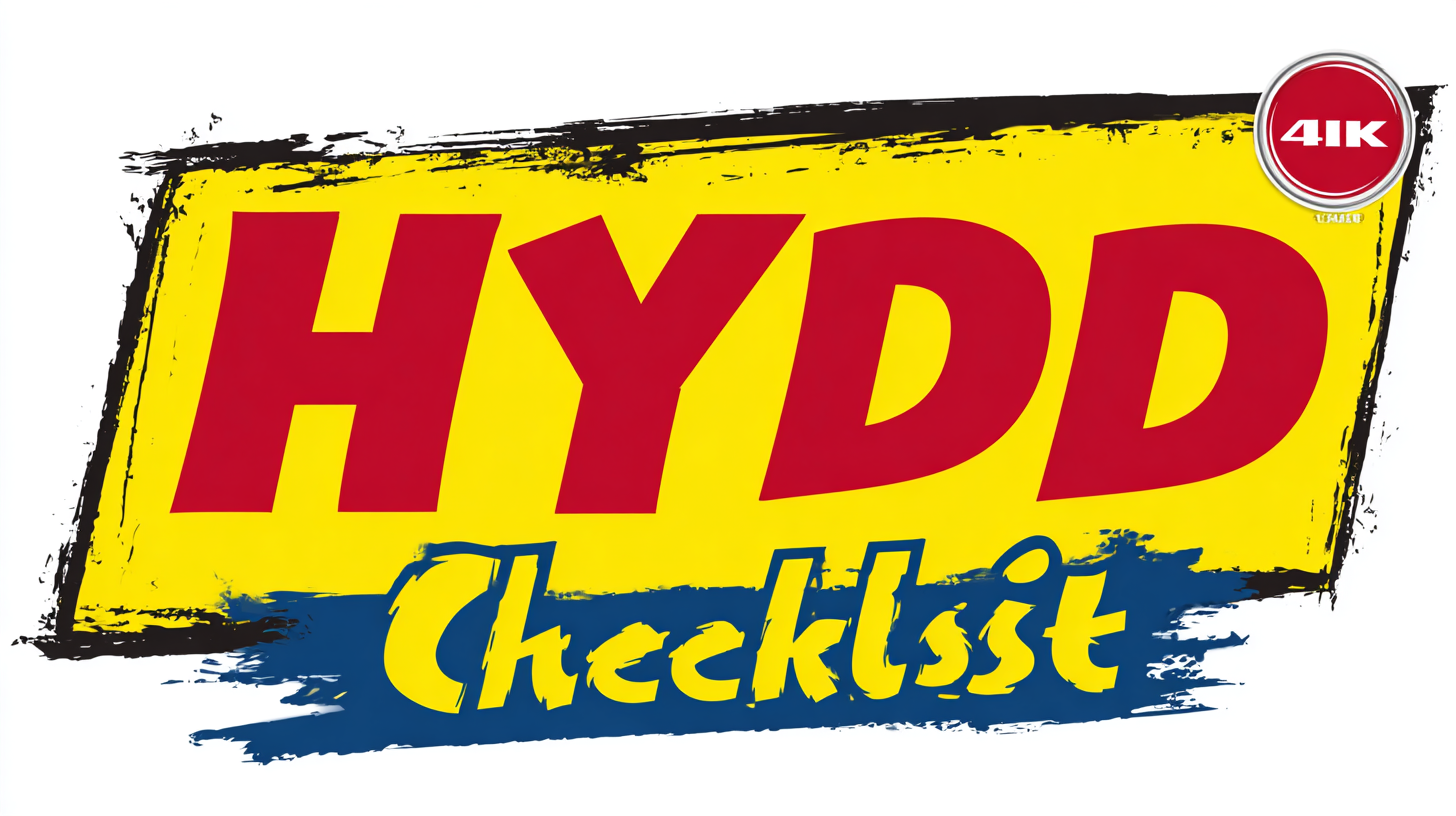
Key Features to Consider When Sourcing Hyd Pumps for Your Projects
When sourcing hydraulic pumps for your projects, it’s crucial to consider several key features that can impact performance and efficiency. Firstly, the pump’s flow rate and pressure rating are essential factors that determine its suitability for a specific application. Pumps with higher flow rates are often preferred for tasks that require significant fluid movement, while those with higher pressure ratings are essential for applications needing forceful pumping action. Understanding the operational requirements of your project will guide you in selecting the pump that meets these demands.
Another critical aspect to consider is the pump's compatibility with the fluids involved in your project. Different materials and designs are available, so it's vital to ensure that the hydraulic pump can handle the specific type of fluid without causing damage or reducing efficiency. Additionally, maintenance requirements and durability should not be overlooked. Investing in a pump that is easy to maintain and has a long lifespan can save you time and money in the long run, making it a smarter choice for your project.
Ultimate Checklist for Sourcing the Best Hyd Pumps for Your Projects - Key Features to Consider When Sourcing Hyd Pumps for Your Projects
Feature | Description | Importance | Typical Range |
---|---|---|---|
Flow Rate | The volume of fluid the pump can move per unit time. | Essential for matching pump capacity with project needs. | 5 - 200 GPM |
Pressure Rating | The maximum pressure the pump can handle safely. | Critical for ensuring system safety and efficiency. | 1500 - 3000 PSI |
Power Source | Type of energy powering the pump (electrical, hydraulic, etc.). | Important for compatibility with project infrastructure. | Electric, Diesel, Hydraulic |
Materials | Type of materials used in the pump construction. | Determines pump durability and resistance to corrosion. | Aluminum, Stainless Steel, Cast Iron |
Size and Weight | Dimensions and weight of the pump. | Affects installation options and transportability. | 20 - 500 lbs |
Seal Type | Type of sealing mechanism to prevent fluid leaks. | Crucial for maintaining system integrity and performance. | Mechanical, Lip Seal, O-ring |
Temperature Range | Operating temperature limits for the pump. | Important for applications involving extreme conditions. | -40°F to 300°F |
Maintenance Requirements | Frequency and type of maintenance needed. | Affects long-term operational costs. | Monthly, Quarterly, Annually |
Evaluating the Efficiency and Performance of Hyd Pumps
When sourcing hydraulic pumps, evaluating their efficiency and performance is paramount to ensure optimal operation and long-term reliability. According to a report by the Hydraulic Institute, efficiency ratings for hydraulic pumps typically range from 75% to 90%, depending on the design and application. It is crucial to consider factors such as flow rate, pressure output, and overall energy consumption when assessing which hydraulic pump will best suit a project's needs.
Moreover, monitoring the performance metrics of hydraulic pumps can provide insights into potential operational issues. A recent study from the International Journal of Fluid Power revealed that a slight decrease in pump efficiency could lead to energy losses exceeding 10%, significantly impacting operational costs. Additionally, proper maintenance and installation best practices can enhance longevity and reduce downtime, making it vital to assess not only pump specifications but also compatibility with existing systems. Investing time in thorough evaluation ensures that the selected hydraulic pump meets both immediate and future project demands.
Cost-Benefit Analysis: Investing in Quality Hyd Pumps
When it comes to sourcing the best hydraulic pumps for your projects, conducting a thorough cost-benefit analysis is essential. Investing in quality hydraulic pumps can significantly impact the efficiency and longevity of your operations. The ongoing expansion in the construction industry, driven by rapid urbanization, highlights the need for reliable pumping solutions that can withstand demanding conditions. Choosing high-quality hydraulic pumps not only ensures superior performance but also reduces the likelihood of costly repairs and downtime in the long run.
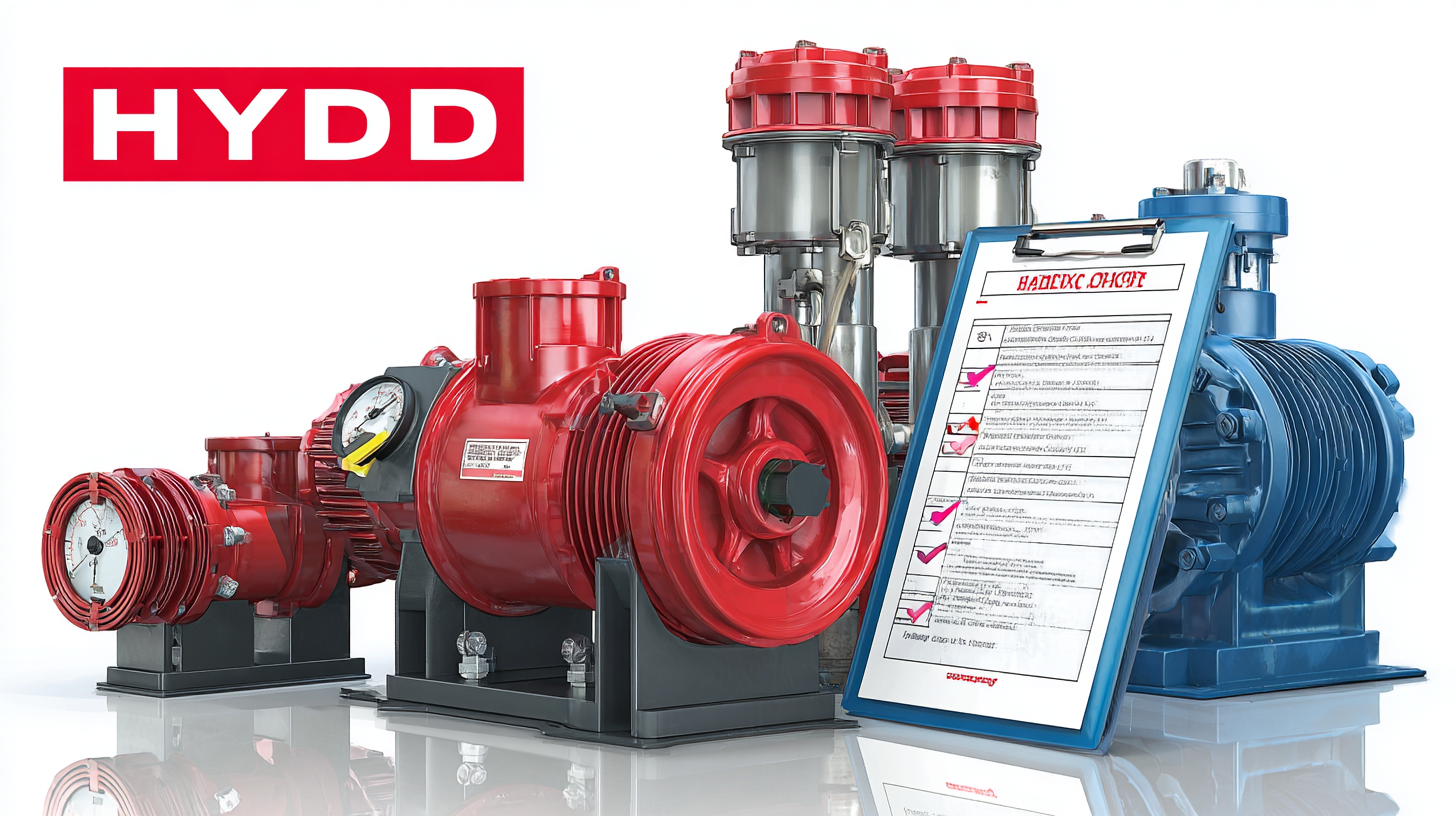
As the global hydraulics market is projected to reach approximately $44.26 billion by 2030, it's crucial to align your investments with industry trends that prioritize sustainability and efficiency. Recognizing this, manufacturers are optimizing production processes to enhance both performance and environmental impact. This shift towards innovative, energy-efficient solutions means that investing in quality hydraulic pumps today can lead to significant operational savings and improved sustainability for your projects in the future. By taking these factors into account, you can make informed sourcing decisions that will benefit your operations both economically and environmentally.
Common Mistakes to Avoid When Selecting Hyd Pumps
When selecting hydraulic pumps for your projects, avoiding common mistakes can save you time and resources. One critical error is neglecting to match the pump type to your specific application. According to the International Fluid Power Society, using the wrong pump configuration can lead to inefficiencies and increased wear, potentially shortening the pump's lifespan by up to 30%. Understanding the intended application—be it mobile machinery or industrial equipment—ensures that you select the appropriate hydraulic pump that will perform optimally.
Another frequent pitfall is underestimating the importance of flow rate and pressure requirements. Failing to accurately assess these parameters can result in inadequate performance or system failures. A study by the National Fluid Power Association emphasized that 60% of hydraulic system issues stem from incorrect flow and pressure assessments. Your project’s success hinges on these calculations—ensuring that the pump can meet the operational demands without straining the system.
Tips: Always consult the manufacturer's specifications and performance charts to verify compatibility with your project needs. Additionally, consider implementing a testing phase with prototypes, if feasible, to gauge the pump's performance under real operating conditions before full-scale implementation. Taking these precautions will significantly reduce the likelihood of costly mistakes.